
directionaldrillingguide

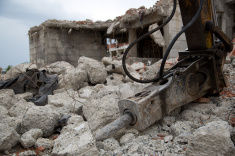
Guidelines On How You Can Make The Most Out Of Horizontal Directional Drilling Equipment
A contractor's job has a sole goal which is to be as profitable as possible. The key to gaining success is to do a job that is efficient and to make sure it is done in the given time frame because, as they say, time is gold. This job is not just for anyone because those who are tasked to operate the machinery and other tools involved in the operation is required to have proper skill, experience, and plan-making abilities.
Its is not beneficial to the contractor if any failure on the equipment or tools occur, regardless how little the issue may be. However, those tool failures that get disclosed are able to help in a way that people are now discovering alternative procedures to achieve drilling success minus the known set backs.
There are unknown hazards that occur in Commercial Directional Drilling San Antonio TX operations that result in complex or unusual conditions which then lead to tooling failure and these hazards are not found in directional drilling. There is a small percentage of failures that are due to faulty practices in the process of production. The key in directional drilling is experience on the job and this is something that cannot be substituted by anything. Expertise in drilling depend on skills and knowledge that is developed over several years of working on the field and this Underground Drilling San Antonio TX should not come as a surprise for this is what most professional endeavors is about.
In horizontal drilling, high PSI application of mud motors are essential. Here are five basic options in the production process for maintaining efficient us of mud motors in the process of directional drilling for extraction of resource.
Keep in mind that you must not stall the motor because this usually indicates that the halt of fluid flow has ceased rotation of the motor. Increasing thrust against a rock or cutting face is usually the cause of motor stalling. When the motor is stalled, fluid is being pushed through the rotor and stator sans any rotation which will then lead to a damaged motor and pump.
Second, abrasives in fluid must be minimized as much as possible and this is done by keeping the screens clean and in perfect condition. Effectiveness is measure through the amount of tolerance the motors and other equipment can handle. During the operations, abrasives move at very high pressures through the motor and this will cause the tool to wear, reduce torque, and overall, reduce its productivity.
It is very important to always perform maintenance at least once a week or every after 100 hours of use for moving parts in motors simply wear out in time.